Miniature connectors
Miniature connectors are used in many applications where SWaP (size, weight and power) is a critical requirement of a solution’s design.
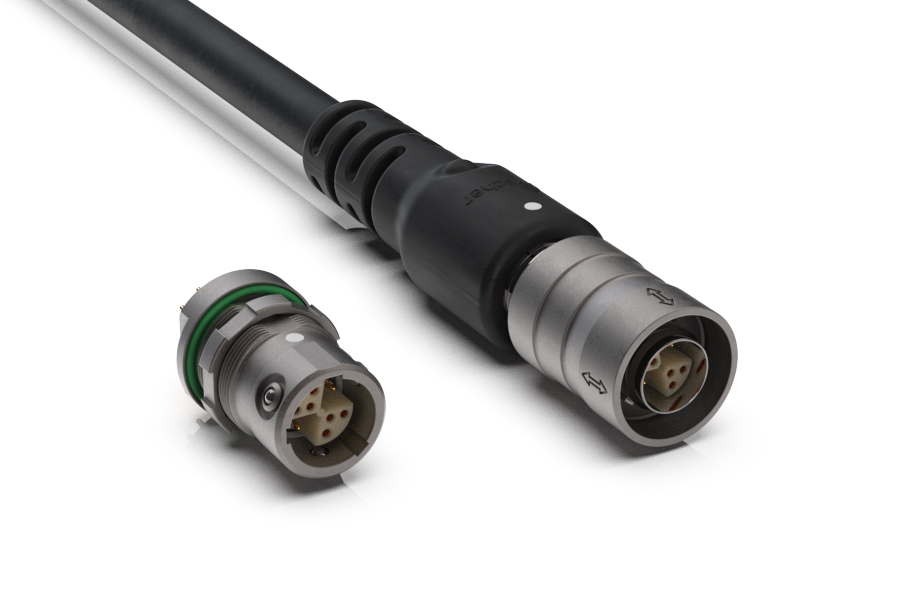
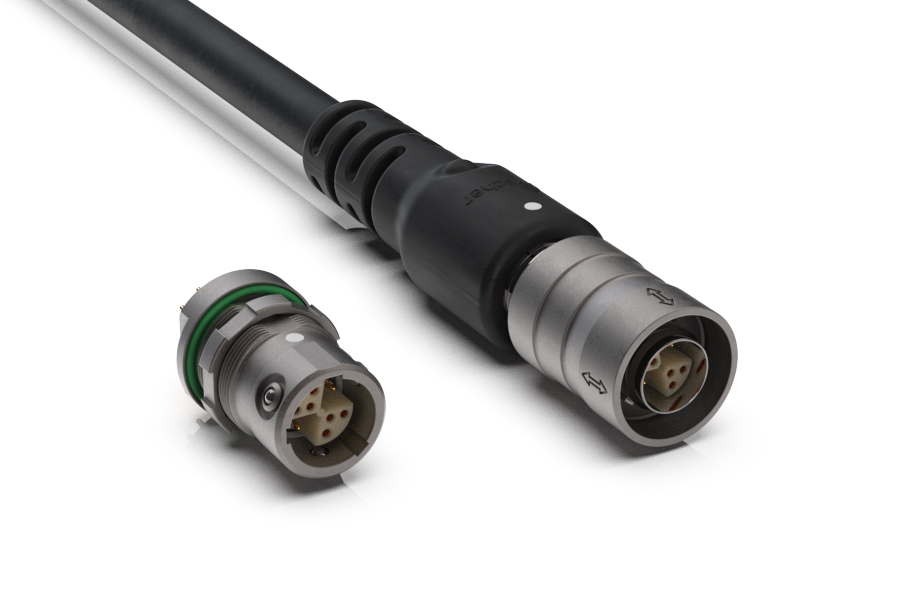
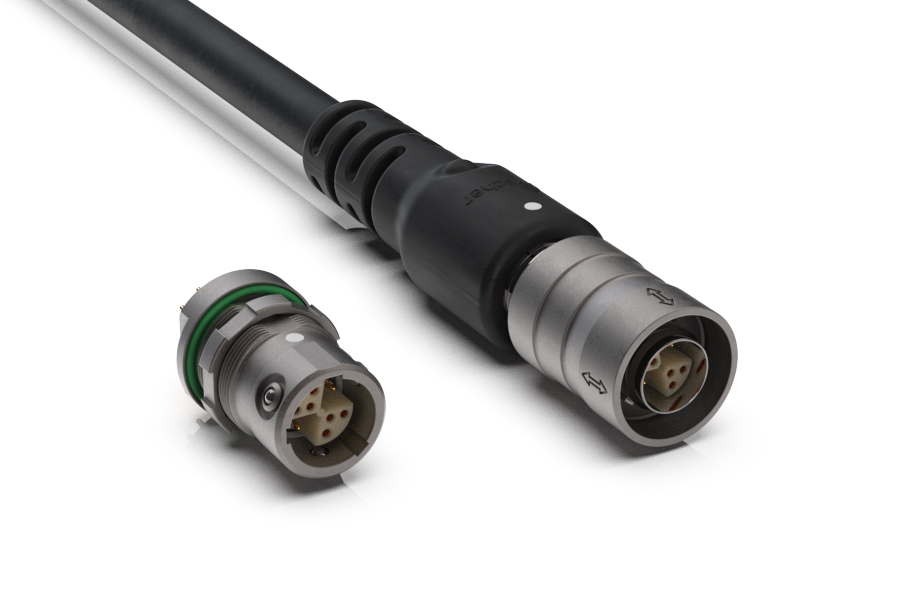
There is not a single industry out there today that isn’t demanding that equipment gets smaller, lighter and more functional at the same time.
Following Moore’s law, the miniaturization of electronics has meant moving away from bulky devices to fully mobile versions, including body-worn electronics.
There is not a single industry out there today that isn’t demanding that equipment gets smaller, lighter and more functional at the same time.
Following Moore’s law, the miniaturization of electronics has meant moving away from bulky devices to fully mobile versions, including body-worn electronics.
There is not a single industry out there today that isn’t demanding that equipment gets smaller, lighter and more functional at the same time.
Following Moore’s law, the miniaturization of electronics has meant moving away from bulky devices to fully mobile versions, including body-worn electronics.
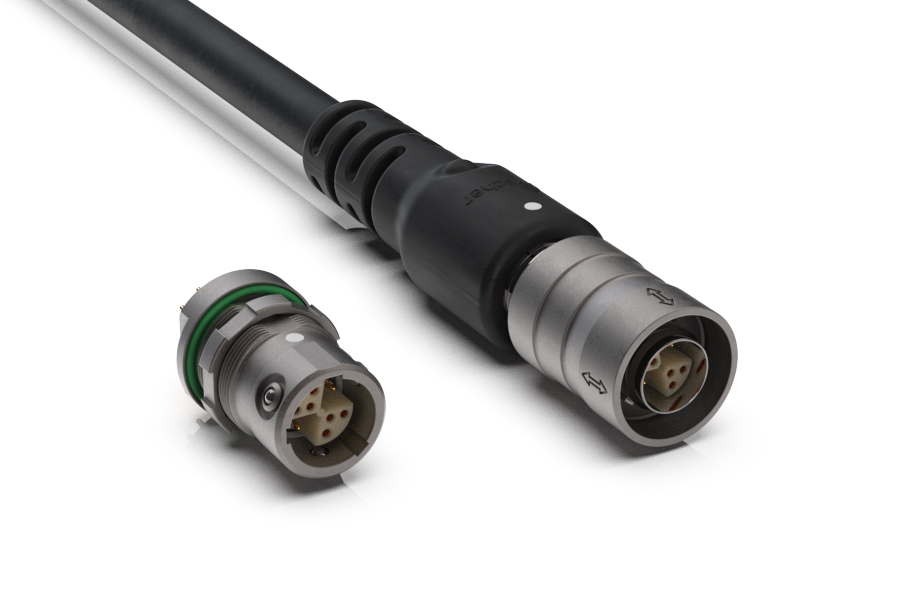
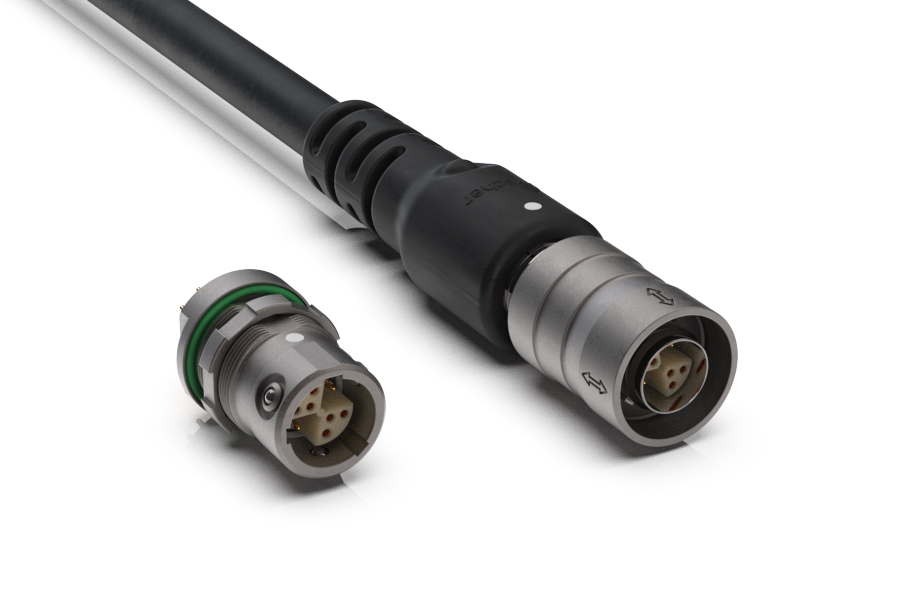
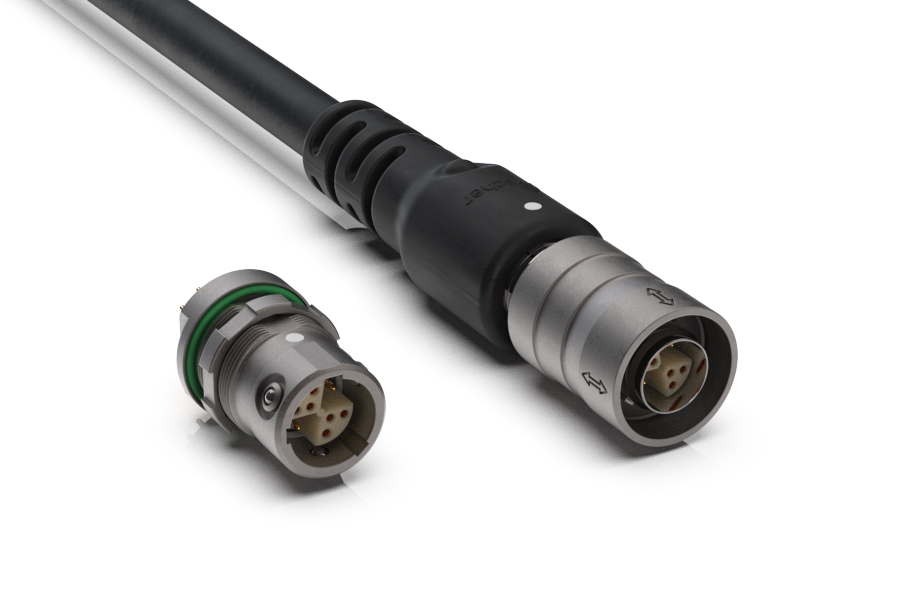
There is not a single industry out there today that isn’t demanding that equipment gets smaller, lighter and more functional at the same time.
Following Moore’s law, the miniaturization of electronics has meant moving away from bulky devices to fully mobile versions, including body-worn electronics.
There is not a single industry out there today that isn’t demanding that equipment gets smaller, lighter and more functional at the same time.
Following Moore’s law, the miniaturization of electronics has meant moving away from bulky devices to fully mobile versions, including body-worn electronics.
There is not a single industry out there today that isn’t demanding that equipment gets smaller, lighter and more functional at the same time.
Following Moore’s law, the miniaturization of electronics has meant moving away from bulky devices to fully mobile versions, including body-worn electronics.
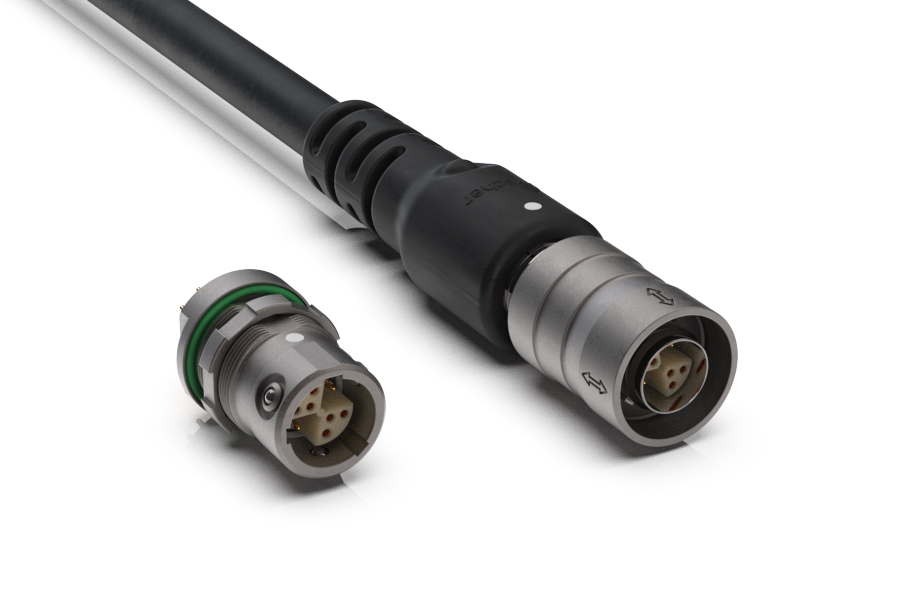
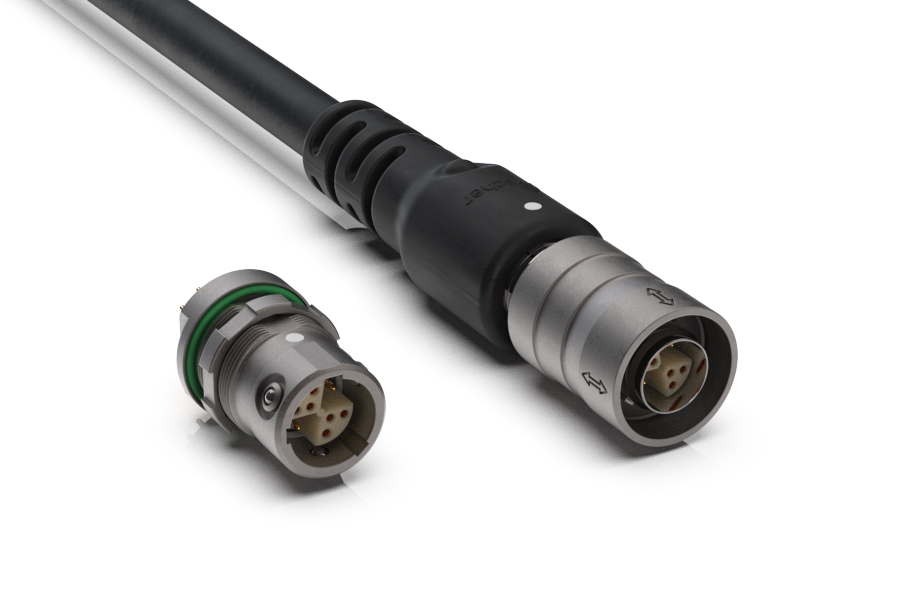
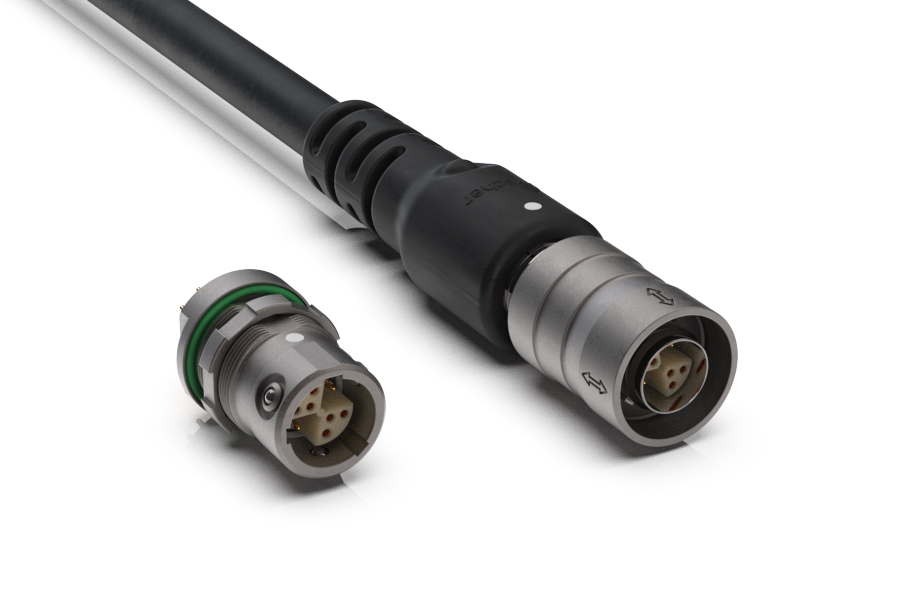
There is not a single industry out there today that isn’t demanding that equipment gets smaller, lighter and more functional at the same time.
Following Moore’s law, the miniaturization of electronics has meant moving away from bulky devices to fully mobile versions, including body-worn electronics.
There is not a single industry out there today that isn’t demanding that equipment gets smaller, lighter and more functional at the same time.
Following Moore’s law, the miniaturization of electronics has meant moving away from bulky devices to fully mobile versions, including body-worn electronics.
There is not a single industry out there today that isn’t demanding that equipment gets smaller, lighter and more functional at the same time.
Following Moore’s law, the miniaturization of electronics has meant moving away from bulky devices to fully mobile versions, including body-worn electronics.
Sales request
Get STEP files and product information
Our miniature connector solutions
Our miniature connectors allow you to move power and/or data (or only power) in ever-smaller devices with lighter, more capable, ultra-miniature solutions – while maximizing ergonomics and robustness.
They increase the performance of your miniature rugged devices, handling mixed signal and power connections in a smaller footprint.
Our miniature connectors allow you to move power and/or data (or only power) in ever-smaller devices with lighter, more capable, ultra-miniature solutions – while maximizing ergonomics and robustness.
They increase the performance of your miniature rugged devices, handling mixed signal and power connections in a smaller footprint.
Our miniature connectors allow you to move power and/or data (or only power) in ever-smaller devices with lighter, more capable, ultra-miniature solutions – while maximizing ergonomics and robustness.
They increase the performance of your miniature rugged devices, handling mixed signal and power connections in a smaller footprint.
Key features
- High-density miniaturization (plug size Ø down to 9 mm)
- Compliance with multiple data transfer protocols (USB 2.0, USB 3.2, Ethernet, Single Pair Ethernet, Audio/UHD Video)
- Sealing level up to IP68/IP69 or hermetic
- Maximum resistance to extreme environmental conditions (temperature, corrosion, shock & vibration, pressure)
- Technical support and assistance
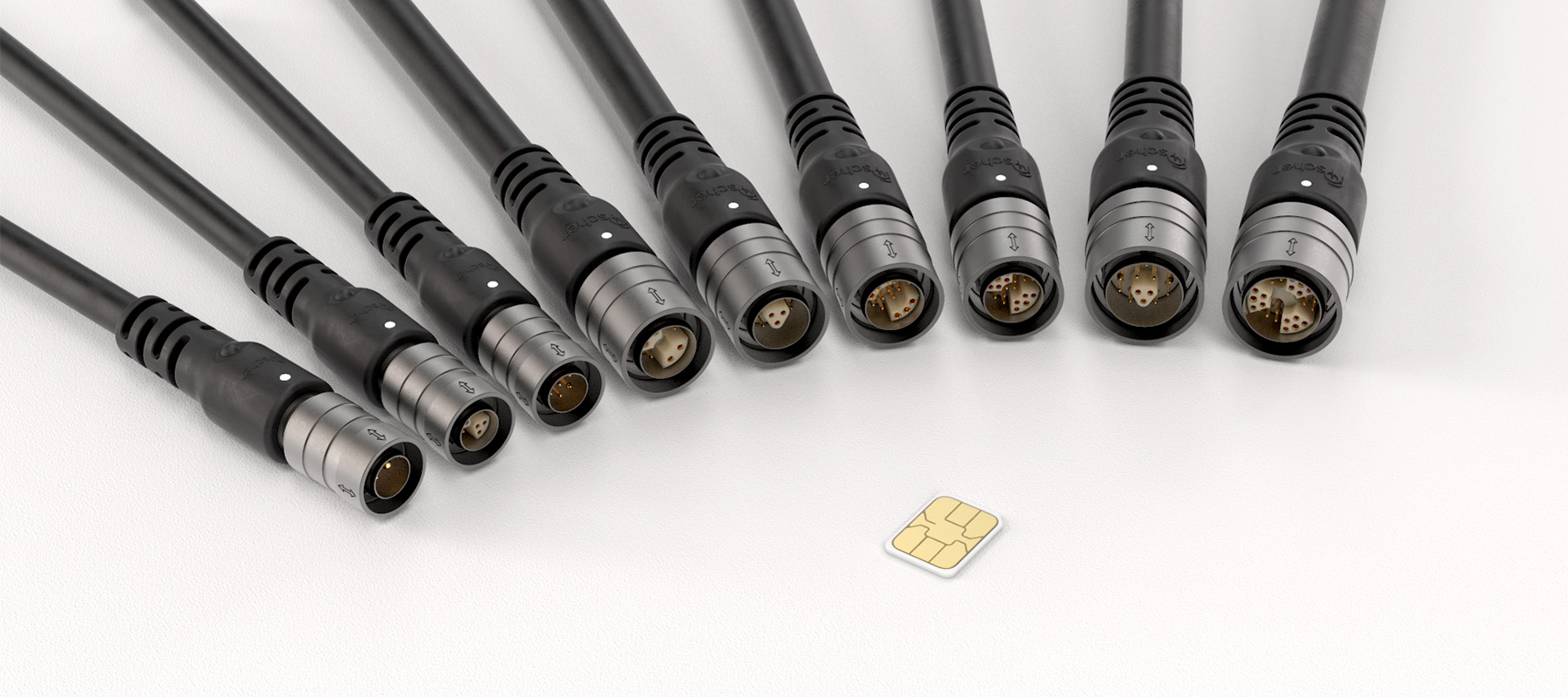
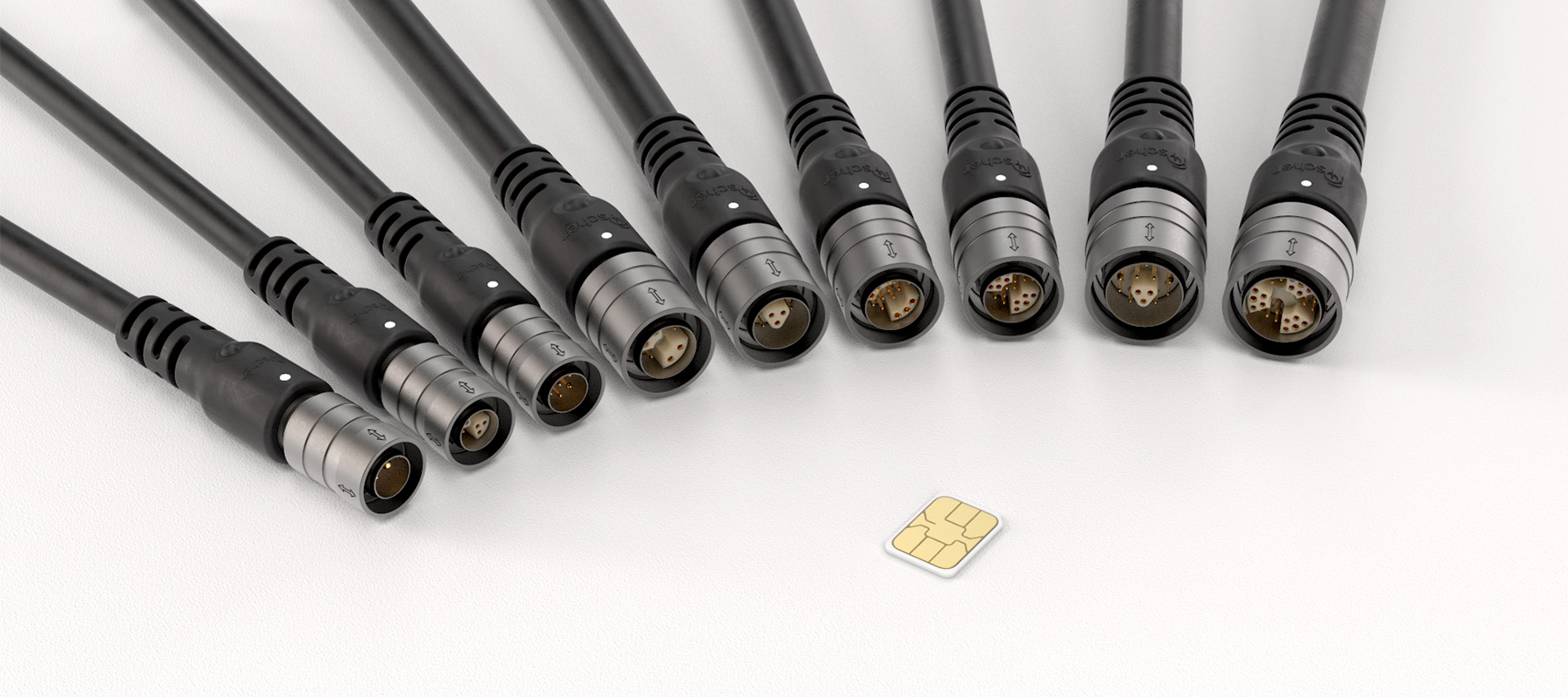
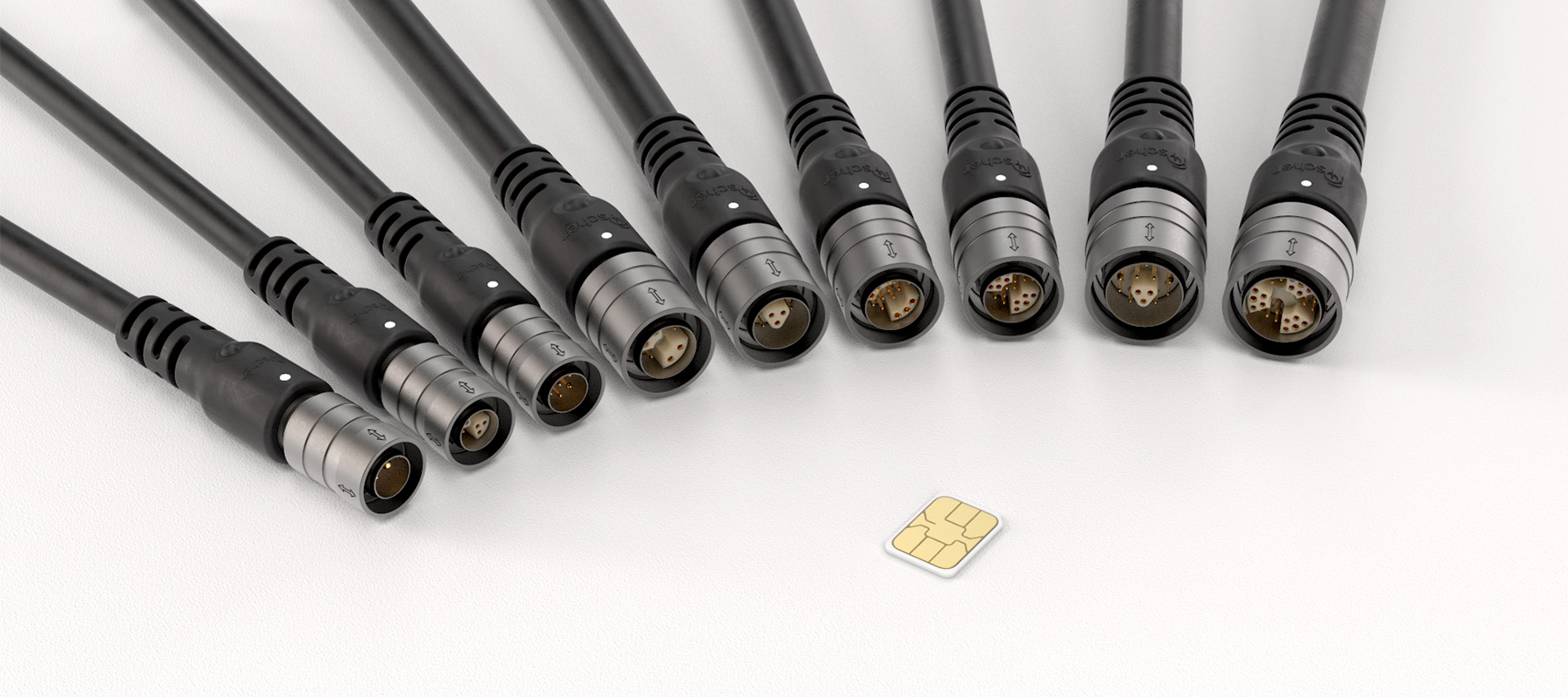
Our product range
Our product range
Our product range
Need other features?
Our custom connector capabilities will help you meet your needs.
Learn more about miniature connectors
Miniature connectors are required for portable, handheld or body-worn applications when space is limited and light weight is critical in industries such as defense & security, instrumentation, testing equipment, civil or military unmanned aerial vehicles (UAVs).
The two main innovation drivers guiding this trend are the multiplication of sensors – reflecting a growing need for data acquisition and transmission – and the constant scale reduction of electronic components.
Miniature connectors are required for portable, handheld or body-worn applications when space is limited and light weight is critical in industries such as defense & security, instrumentation, testing equipment, civil or military unmanned aerial vehicles (UAVs).
The two main innovation drivers guiding this trend are the multiplication of sensors – reflecting a growing need for data acquisition and transmission – and the constant scale reduction of electronic components.
Miniature connectors are required for portable, handheld or body-worn applications when space is limited and light weight is critical in industries such as defense & security, instrumentation, testing equipment, civil or military unmanned aerial vehicles (UAVs).
The two main innovation drivers guiding this trend are the multiplication of sensors – reflecting a growing need for data acquisition and transmission – and the constant scale reduction of electronic components.
How to choose the right miniature connector?
How to choose the right miniature connector?
How to choose the right miniature connector?
To make the right choice among various miniature connector offers, you need to consider a large set of variables.
To make the right choice among various miniature connector offers, you need to consider a large set of variables.
To make the right choice among various miniature connector offers, you need to consider a large set of variables.
1. Electrical needs
Defining the electrical voltage and current requirements each contact will carry is the first step to selecting the ideal miniature connectors for your device. In order to ensure the application functions properly, it is necessary to confirm not only that the correct number of contacts are in place, but also that they are capable of withstanding the required voltage and current levels, as well as adhering to the specific communication data protocol layout requirements.
The size of the contact and the size of the wire dictate the current-carrying capability of a contact. Contact spacing, insulation materials, and the geometry of the insulator used to isolate the contacts dictate the voltage rating.
2. Data speed
Focus on data speed has increased significantly over the past few years, with devices expected to communicate massive amounts of data via specific protocols, over local area networks, and through the Internet to other connected devices. Often, when it comes to critical applications that rugged miniature connectors are used in, data transfer not only has to be accurate without interference, but it must also be fast enough to trigger actions in fractions of seconds to ensure the safety of equipment and people.
3. Termination types
Miniature connectors with solder contacts are typically easier to seal against moisture ingress, while crimp contacts may offer better field reparability. There is a trade-off between the two, so the final decision on which termination type to use is often made after discussions with your manufacturing and design groups. It is important to know exactly how and where the connector will be used, and whether field reparability is a requirement, as this decision has a significant impact on the assembly equipment and processes used in manufacturing.
1. Electrical needs
Defining the electrical voltage and current requirements each contact will carry is the first step to selecting the ideal miniature connectors for your device. In order to ensure the application functions properly, it is necessary to confirm not only that the correct number of contacts are in place, but also that they are capable of withstanding the required voltage and current levels, as well as adhering to the specific communication data protocol layout requirements.
The size of the contact and the size of the wire dictate the current-carrying capability of a contact. Contact spacing, insulation materials, and the geometry of the insulator used to isolate the contacts dictate the voltage rating.
2. Data speed
Focus on data speed has increased significantly over the past few years, with devices expected to communicate massive amounts of data via specific protocols, over local area networks, and through the Internet to other connected devices. Often, when it comes to critical applications that rugged miniature connectors are used in, data transfer not only has to be accurate without interference, but it must also be fast enough to trigger actions in fractions of seconds to ensure the safety of equipment and people.
3. Termination types
Miniature connectors with solder contacts are typically easier to seal against moisture ingress, while crimp contacts may offer better field reparability. There is a trade-off between the two, so the final decision on which termination type to use is often made after discussions with your manufacturing and design groups. It is important to know exactly how and where the connector will be used, and whether field reparability is a requirement, as this decision has a significant impact on the assembly equipment and processes used in manufacturing.
1. Electrical needs
Defining the electrical voltage and current requirements each contact will carry is the first step to selecting the ideal miniature connectors for your device. In order to ensure the application functions properly, it is necessary to confirm not only that the correct number of contacts are in place, but also that they are capable of withstanding the required voltage and current levels, as well as adhering to the specific communication data protocol layout requirements.
The size of the contact and the size of the wire dictate the current-carrying capability of a contact. Contact spacing, insulation materials, and the geometry of the insulator used to isolate the contacts dictate the voltage rating.
2. Data speed
Focus on data speed has increased significantly over the past few years, with devices expected to communicate massive amounts of data via specific protocols, over local area networks, and through the Internet to other connected devices. Often, when it comes to critical applications that rugged miniature connectors are used in, data transfer not only has to be accurate without interference, but it must also be fast enough to trigger actions in fractions of seconds to ensure the safety of equipment and people.
3. Termination types
Miniature connectors with solder contacts are typically easier to seal against moisture ingress, while crimp contacts may offer better field reparability. There is a trade-off between the two, so the final decision on which termination type to use is often made after discussions with your manufacturing and design groups. It is important to know exactly how and where the connector will be used, and whether field reparability is a requirement, as this decision has a significant impact on the assembly equipment and processes used in manufacturing.
4. Environmental or hermetic sealing
If the miniature connectors will be used in harsh operating environments, check the manufacturer’s IP (Ingress Protection) rating for sealing to dust and water at various depths and operating time frames. Make sure you understand the end-use environment for your miniature connectors and then compare that scenario with the details behind the manufacturer’s IP rating.
5. Materials
Selecting the housing material wisely is critical, as this will impact resistance, reliability, weight, and cost. Brass connectors with nickel/chrome plating are traditionally more robust and have longer lifecycles than many other materials. For improved corrosion resistance, you may choose stainless steel, and if weight is an issue, aluminum connectors may be an option. Brass and aluminum are the most preferred materials for rugged miniature connectors.
6. Reliability needs
If you require a very high number of mating cycles, consider a miniature connector with 5,000 to 10,000 mating cycles. This is especially important if a failed electrical connection can put lives at risk, such as in medical or military environments. There may be trade-offs to consider between miniaturization and the number of mating cycles, as miniaturization often means fewer mating cycles.
7. Miniaturization
Everything that we have talked about so far will have an influence on the size limitations and functional requirements of your miniature connector. Currently, impressive advancements are being made in the sphere of miniaturization that you should capitalize on whenever possible. In fact, it is now feasible to create a single miniature connector for a particular purpose that previously would have necessitated two or three connectors.
4. Environmental or hermetic sealing
If the miniature connectors will be used in harsh operating environments, check the manufacturer’s IP (Ingress Protection) rating for sealing to dust and water at various depths and operating time frames. Make sure you understand the end-use environment for your miniature connectors and then compare that scenario with the details behind the manufacturer’s IP rating.
5. Materials
Selecting the housing material wisely is critical, as this will impact resistance, reliability, weight, and cost. Brass connectors with nickel/chrome plating are traditionally more robust and have longer lifecycles than many other materials. For improved corrosion resistance, you may choose stainless steel, and if weight is an issue, aluminum connectors may be an option. Brass and aluminum are the most preferred materials for rugged miniature connectors.
6. Reliability needs
If you require a very high number of mating cycles, consider a miniature connector with 5,000 to 10,000 mating cycles. This is especially important if a failed electrical connection can put lives at risk, such as in medical or military environments. There may be trade-offs to consider between miniaturization and the number of mating cycles, as miniaturization often means fewer mating cycles.
7. Miniaturization
Everything that we have talked about so far will have an influence on the size limitations and functional requirements of your miniature connector. Currently, impressive advancements are being made in the sphere of miniaturization that you should capitalize on whenever possible. In fact, it is now feasible to create a single miniature connector for a particular purpose that previously would have necessitated two or three connectors.
4. Environmental or hermetic sealing
If the miniature connectors will be used in harsh operating environments, check the manufacturer’s IP (Ingress Protection) rating for sealing to dust and water at various depths and operating time frames. Make sure you understand the end-use environment for your miniature connectors and then compare that scenario with the details behind the manufacturer’s IP rating.
5. Materials
Selecting the housing material wisely is critical, as this will impact resistance, reliability, weight, and cost. Brass connectors with nickel/chrome plating are traditionally more robust and have longer lifecycles than many other materials. For improved corrosion resistance, you may choose stainless steel, and if weight is an issue, aluminum connectors may be an option. Brass and aluminum are the most preferred materials for rugged miniature connectors.
6. Reliability needs
If you require a very high number of mating cycles, consider a miniature connector with 5,000 to 10,000 mating cycles. This is especially important if a failed electrical connection can put lives at risk, such as in medical or military environments. There may be trade-offs to consider between miniaturization and the number of mating cycles, as miniaturization often means fewer mating cycles.
7. Miniaturization
Everything that we have talked about so far will have an influence on the size limitations and functional requirements of your miniature connector. Currently, impressive advancements are being made in the sphere of miniaturization that you should capitalize on whenever possible. In fact, it is now feasible to create a single miniature connector for a particular purpose that previously would have necessitated two or three connectors.
Example of high-performance miniature connector applications
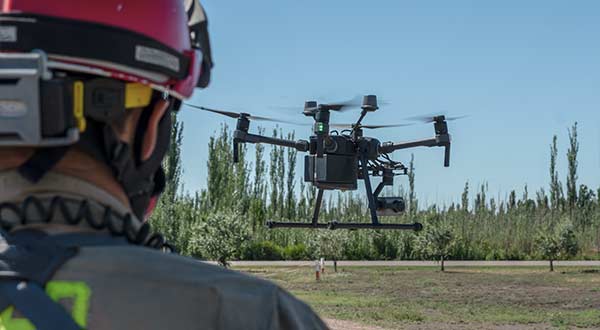
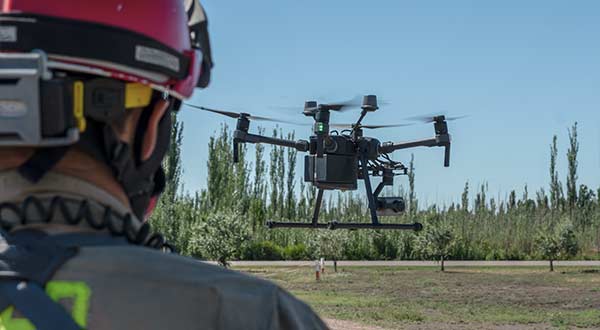
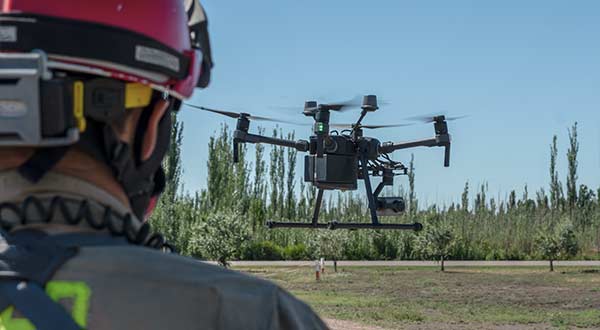
Drones
Unmanned aerial vehicles (UAVs) and the tools and applications they carry, e.g., Lidar for drones, are designed to be small and lightweight, which means that every component must also share those characteristics. Miniature connectors help save space and reduce weight.
To ensure the proper functioning of the drone, the components must resist vibrations, environmental factors such as extreme temperatures, and exposure to rain, sand, and dust.
Drones
Unmanned aerial vehicles (UAVs) and the tools and applications they carry, e.g., Lidar for drones, are designed to be small and lightweight, which means that every component must also share those characteristics. Miniature connectors help save space and reduce weight.
To ensure the proper functioning of the drone, the components must resist vibrations, environmental factors such as extreme temperatures, and exposure to rain, sand, and dust.
Drones
Unmanned aerial vehicles (UAVs) and the tools and applications they carry, e.g., Lidar for drones, are designed to be small and lightweight, which means that every component must also share those characteristics. Miniature connectors help save space and reduce weight.
To ensure the proper functioning of the drone, the components must resist vibrations, environmental factors such as extreme temperatures, and exposure to rain, sand, and dust.
Miniaturization explained
Increased density
Increasing density means either offering more functionality and performance in a similar footprint or offering similar functionality and performance but within a reduced and minimized footprint – or even getting the best of both worlds.
One way of achieving higher density involves replacing traditional multiple connectors with a single one that combines various channels of the same type (e.g. data) and/or mixing various types of contact. Such combinations yield enhanced flexibility when it comes to device and printed-circuit-board integration.
For connectivity using copper, examples of hybrid configurations include: combining signal and power contacts (up to 24 contacts of 0.5 mm diameter in a receptacle diameter of 12 mm for our ultra-miniature Fischer MiniMax™ Series); or even signal, power, fluidic and coax contacts. For optical transmission, combining fiber and copper termini (for power or data) is particularly effective.
Another example of adding extra functionality or performance within a similar package is integrating transceivers within the cable – this enables the elimination of bulky additional devices to translate protocols. A typical example of such a data transmission enhancement is translating an Ethernet signal from one end of the cable into a USB signal on the other end.
Our quest to reach higher density and deliver more within a reduced size package has also led us to explore higher data-transmission rates up to 10 Gbit/s and adopt new data protocols such as the Single Pair Ethernet (SPE). The SPE allows an ethernet signal with data rates of up to 1 Gbit/s to be transmitted over a single twisted pair – instead of standard Ethernet transmission that requires a minimum of 8 contacts.
Increased density
Increasing density means either offering more functionality and performance in a similar footprint or offering similar functionality and performance but within a reduced and minimized footprint – or even getting the best of both worlds.
One way of achieving higher density involves replacing traditional multiple connectors with a single one that combines various channels of the same type (e.g. data) and/or mixing various types of contact. Such combinations yield enhanced flexibility when it comes to device and printed-circuit-board integration.
For connectivity using copper, examples of hybrid configurations include: combining signal and power contacts (up to 24 contacts of 0.5 mm diameter in a receptacle diameter of 12 mm for our ultra-miniature Fischer MiniMax™ Series); or even signal, power, fluidic and coax contacts. For optical transmission, combining fiber and copper termini (for power or data) is particularly effective.
Another example of adding extra functionality or performance within a similar package is integrating transceivers within the cable – this enables the elimination of bulky additional devices to translate protocols. A typical example of such a data transmission enhancement is translating an Ethernet signal from one end of the cable into a USB signal on the other end.
Our quest to reach higher density and deliver more within a reduced size package has also led us to explore higher data-transmission rates up to 10 Gbit/s and adopt new data protocols such as the Single Pair Ethernet (SPE). The SPE allows an ethernet signal with data rates of up to 1 Gbit/s to be transmitted over a single twisted pair – instead of standard Ethernet transmission that requires a minimum of 8 contacts.
Increased density
Increasing density means either offering more functionality and performance in a similar footprint or offering similar functionality and performance but within a reduced and minimized footprint – or even getting the best of both worlds.
One way of achieving higher density involves replacing traditional multiple connectors with a single one that combines various channels of the same type (e.g. data) and/or mixing various types of contact. Such combinations yield enhanced flexibility when it comes to device and printed-circuit-board integration.
For connectivity using copper, examples of hybrid configurations include: combining signal and power contacts (up to 24 contacts of 0.5 mm diameter in a receptacle diameter of 12 mm for our ultra-miniature Fischer MiniMax™ Series); or even signal, power, fluidic and coax contacts. For optical transmission, combining fiber and copper termini (for power or data) is particularly effective.
Another example of adding extra functionality or performance within a similar package is integrating transceivers within the cable – this enables the elimination of bulky additional devices to translate protocols. A typical example of such a data transmission enhancement is translating an Ethernet signal from one end of the cable into a USB signal on the other end.
Our quest to reach higher density and deliver more within a reduced size package has also led us to explore higher data-transmission rates up to 10 Gbit/s and adopt new data protocols such as the Single Pair Ethernet (SPE). The SPE allows an ethernet signal with data rates of up to 1 Gbit/s to be transmitted over a single twisted pair – instead of standard Ethernet transmission that requires a minimum of 8 contacts.
Optimized packaging factors
To optimize density, our experts consider devices’ footprints in terms of volume and size, without compromising our solutions’ robustness, ergonomics and conductivity performances.
Key dimensional factors include low-profile design and reduced diameters for our connectivity solutions.
- The ‘flat’, right-angle design of the Fischer Freedom™ Series can halve the protruding dimensions of more traditional right-angle solutions.
- The ultra-miniature Fischer MiniMax™ Series offers up to 24 contacts for a 12 mm diameter receptacle, representing up to a 45% space saving compared to standard receptacles with a similar number of contacts, while achieving an IP68 sealing rating over up to 5,000 mating cycles.
The external dimensions of electronic devices are affected by the growing demand for mobile (or wearable) electronics as well as for autonomous robotics and vehicles. This implies ever-lighter components. With up to 75% weight saving, the Fischer MiniMax™ Series achieves both size and weight reduction, maximizing performances while minimizing the integration burden.
Optimized packaging factors
To optimize density, our experts consider devices’ footprints in terms of volume and size, without compromising our solutions’ robustness, ergonomics and conductivity performances.
Key dimensional factors include low-profile design and reduced diameters for our connectivity solutions.
- The ‘flat’, right-angle design of the Fischer Freedom™ Series can halve the protruding dimensions of more traditional right-angle solutions.
- The ultra-miniature Fischer MiniMax™ Series offers up to 24 contacts for a 12 mm diameter receptacle, representing up to a 45% space saving compared to standard receptacles with a similar number of contacts, while achieving an IP68 sealing rating over up to 5,000 mating cycles.
The external dimensions of electronic devices are affected by the growing demand for mobile (or wearable) electronics as well as for autonomous robotics and vehicles. This implies ever-lighter components. With up to 75% weight saving, the Fischer MiniMax™ Series achieves both size and weight reduction, maximizing performances while minimizing the integration burden.
Optimized packaging factors
To optimize density, our experts consider devices’ footprints in terms of volume and size, without compromising our solutions’ robustness, ergonomics and conductivity performances.
Key dimensional factors include low-profile design and reduced diameters for our connectivity solutions.
- The ‘flat’, right-angle design of the Fischer Freedom™ Series can halve the protruding dimensions of more traditional right-angle solutions.
- The ultra-miniature Fischer MiniMax™ Series offers up to 24 contacts for a 12 mm diameter receptacle, representing up to a 45% space saving compared to standard receptacles with a similar number of contacts, while achieving an IP68 sealing rating over up to 5,000 mating cycles.
The external dimensions of electronic devices are affected by the growing demand for mobile (or wearable) electronics as well as for autonomous robotics and vehicles. This implies ever-lighter components. With up to 75% weight saving, the Fischer MiniMax™ Series achieves both size and weight reduction, maximizing performances while minimizing the integration burden.